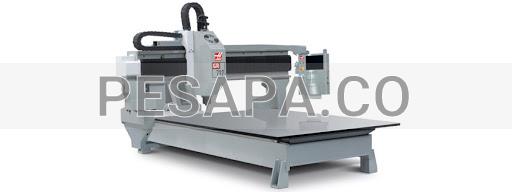
History and components of CNC machine
History of machines Numerical control
After World War II, the need for devices capable of making sophisticated and precise parts for the aerospace industry was felt before 1949; In 1949, Parsons signed its first contract with the US Air Force to build the first NC numerically controlled device. In 1951 the project was awarded to the Massachusetts Institute of Technology (MIT).
In 1952, the Massachusetts Institute of Technology’s Serum Mechanism Laboratory began its research efforts, and the first NC milling machine made great efforts to develop more advanced control devices. With the advent of computers in NC systems, another change in NC technology took place. Today, CNC machines with a greater number of axes, more control, and better accuracy and speed can be seen at very high levels of automation in DNC, CAD / CAM and CIMS systems.
Numerical control (NC)
Numerical control is the use of encrypted codes of numbers, letters, and symbols that are intelligible to the control unit and, after decoding, are converted into electrical pulses, current, and these pulses are used to turn the machine on and off. It becomes. The philosophy behind NC machines is not only the need for the ability to make complex parts, but also the creation of automation and automation.
Humans have always strived to mechanize production because automation can improve the quality and quantity of productivity of human activities and also allows a small number of professionals to achieve the results that they can achieve. The past required the participation of a large number of experienced people. Automated systems, on the other hand, make it possible to do things that go beyond human capabilities.
Computer numerical control
Computer Numerical Control (CNC) is an NC system based on the use of a computer as a control unit. In these “controls”, the speed of data processing is very high due to the use of computers, and unlike NC machines, which read programs line by line, it is able to read and check all program lines and then execute its high speed and flexibility with CNC machines and it gives them the courage to try what they have in mind as soon as possible and to think about improving their product and to meet the needs of their customers quickly and to adapt to the needs of the market as soon as possible.
Main components of CNC machines
Machine program (input unit)
The program contains a set of numbers, letters, and symbols that tell the machine what to do. The set of numbers, letters and symbols, which are encrypted in code, are interpreted by the Machine Control Unit (CNU). In addition to workpiece path information, the program includes information on technology (speed and progress values) and auxiliary information (such as turning on and off three systems, switching on and off the cooling fluid flow. The program can, in addition to typing directly through the device keyboard) MDI) is sent to the machine via perforated tape, magnetic tape, magnetic disk and computer (DNC).
Car control unit
CNC is a type of control used on machines and software for automation, and each control system has three main components: input unit, processor unit, and output unit.
The most complex control system is man, in which the five senses function as the input unit, the human brain, as the processor, and the human muscles and speech as the output unit.
In CNC, the three main components of the cut letter and the title of the input unit, the processor unit and the output unit. The components of the control unit are: tape reader, CPU microprocessor, RAM, ROM, Buffers, PHC, amplifier, control panel Operations that are very simple for humans, such as reading size, distinguishing between numbers, letters, and symbols, are very difficult for electronic, computer, and computer equipment, so the information entering the machine must be encrypted for quick and easy recognition.
Information signals have one of the following four states.
1-Analog or continuous signal:
Human verbal signals, thermometers, pressure gauges are such signals and it is very difficult to work with these signals.
2-Discrete or discrete signal:
Is a signal whose values have constant values over a period of time equal to these values. These values have no relation to each other. The best example for the signals above is a statistical example.
3-Digital signal or step:
It is a discrete or discrete type of signal, except that its values change by a certain ratio. Telecommunication systems work with digital signals.
4-Binary signal or two-sided:
It is a kind of digital signal, except that its values change only between the two zeros and ones. Like a switch, it has two open-state states, which are considered zero in the open state and one in the closed state. The signals most commonly used in engineering are digital signals, most of which are considered to be part of these signals. Binary signals are very valuable in presenting information because in control they can be easily displayed, as well as mathematical operations can be easily done with them. Numbers of letters and symbols can be easily encoded with these signals. In Boolean algebra, which uses only two numbers zero and one, unlike general algebra, which uses numbers from the spectrum and range, the logical operations Not, AND, NOR, and NAND can be written in mathematical language and used in control technology. A computer is an electrical device that works with voltage. If a computer is built based on decimal numbers (analog), it needs tens of different voltages to identify the numbers 9…, 2, 1, and 0, which is very expensive and difficult to do. We need a voltage unit, which can have two modes of voltage presence (one) and no voltage. Numbers in binary chain systems are from zero to one, which are standardized in two types of ISO and EIA.
Machinery
The third main part of a CNC system is the machine tool, which performs the main work of the process, i.e., chipping. This part actually includes the workpiece, tool, fixture and other mechanical and electrical components in the CNC machine. The machine tools are also divided into several groups.
1-Machines in which the workpiece has rotational motion and the tool has linear motion, such as CNC lathe.
2-Machines in which the workpiece has a linear motion and a rotary motion tool such as a CNC milling machine.
3-Machines in which chipping is done by electric discharge method.
4-Machines that use abrasive chips, such as CNC stone.
Mechanical and electrical components, CNC machines
car body:
It is a part of a machine on which other surface components are mounted, so it must be very strong and resistant to vibration and heat to withstand high accelerations and speeds, mainly made of gray cast iron, hardened, and in some cases made of ceramic or graphite.
Sliders:
The plates are smooth and hard, with the tool holder or table sliding on the roller and lubrication system to reduce friction, the sliders being coated, or the surface of a thin layer of oil or cushion moving through the air.
Main axis:
The main motor rotates the workpiece in the lathe and the tool in the milling machine. In both cases, the motor must provide the power needed to cut the workpiece. The main motor can be of DC type for cars and small robots, or of three-phase AC type for higher power. In the latter type, we need the help of a special drive to create different speeds.
Types of motors, actuators, axles
CNC machines use electric, hydraulic, and pneumatic actuators to move and advance the axes. Numerically controlled actuators are used, each of which is described in detail. He named electricity consumption, maintenance.
Electrical stimuli
Electrical actuators include AC, DC, or stepper motors.
-
A) DC motors (DC)
In this type of motor, the rotor is driven by magnetic field, stator or electric current. The rotational speeds of these motors can be well controlled by changing the voltage as well as the torque of the motor with the amount of input current. Fast, relative to changes, speed, and… are most used in CNC machines. These motors are not used in open circuits, but they are widely used in closed circuits. These motors are mostly used for the main cycle of three systems.
-
B) AC motors
In this type of motor, the rotational speed is alternated by changing the input frequency, and the only advantage of these motors is that they do not need a rectifier and because of their large volume, they are less used in CNC machines than DC motors. Axes are used.
-
C) stepper motors
In these motors, by giving each input control pulse, the motors rotate to a specific angle called the step angle, and rotate according to the angle of the rotating ball, which causes the linear motion of the nut to rotate at the desired speed. It is and by increasing the number of poles can increase their accuracy. Characteristics of these motors are low volume, precise control of axles and their cheapness, and their disadvantage is their low power. These types of motors are used in open circuit systems. Tool Changer is used in small numerical control machines.
Hydraulic actuators
In hydraulic actuators, cylinders and pistons are used for short lengths, and hydraulic motors are used for long lengths. They have low weight and volume and can be used in hazardous environments. Also, hydraulic actuators have a uniform motion and are not stepped.
Pneumatic actuators
The performance of these actuators is similar to that of hydraulic actuators, and they are less accurate than their advantages.
BALL SCREW
A ball screw is commonly used to ensure the movement of the shafts (table or tool holder). In this way, between the bolt and the nut, the error occurs, not slipping, and despite the precise bullets, the direction of motion is minimized when reversed, resulting in very smooth and precise movement, so that the machine can be moved easily. It gave 0.001 mm and everyone expected accurate movement.
Axis position measurement systems (ENCODER)
Encoder is used to control the position of the axes. In this mechanism, a glass disk with dark and light lines designed along it is placed along the axis, one light source on one side of the screen and one or more light sensors on the other side. They always move with the axis. During the rotation of the axis, the path of light is cut and connected by dark lines on the disk, and the optical cell transmits the output voltage based on the intensity of the light, and as a result the photocell sends a sinusoidal wave that transforms this source into one. And the output pulses are counted, from which the displacement of the axes is calculated. In this type of measurement system, the glass plate is usually circular, called angular encoders, and mounts on the axis of the ball screw and rotates with it. These encoders are smaller and easier to maintain. In addition, the linear encoder is also used.